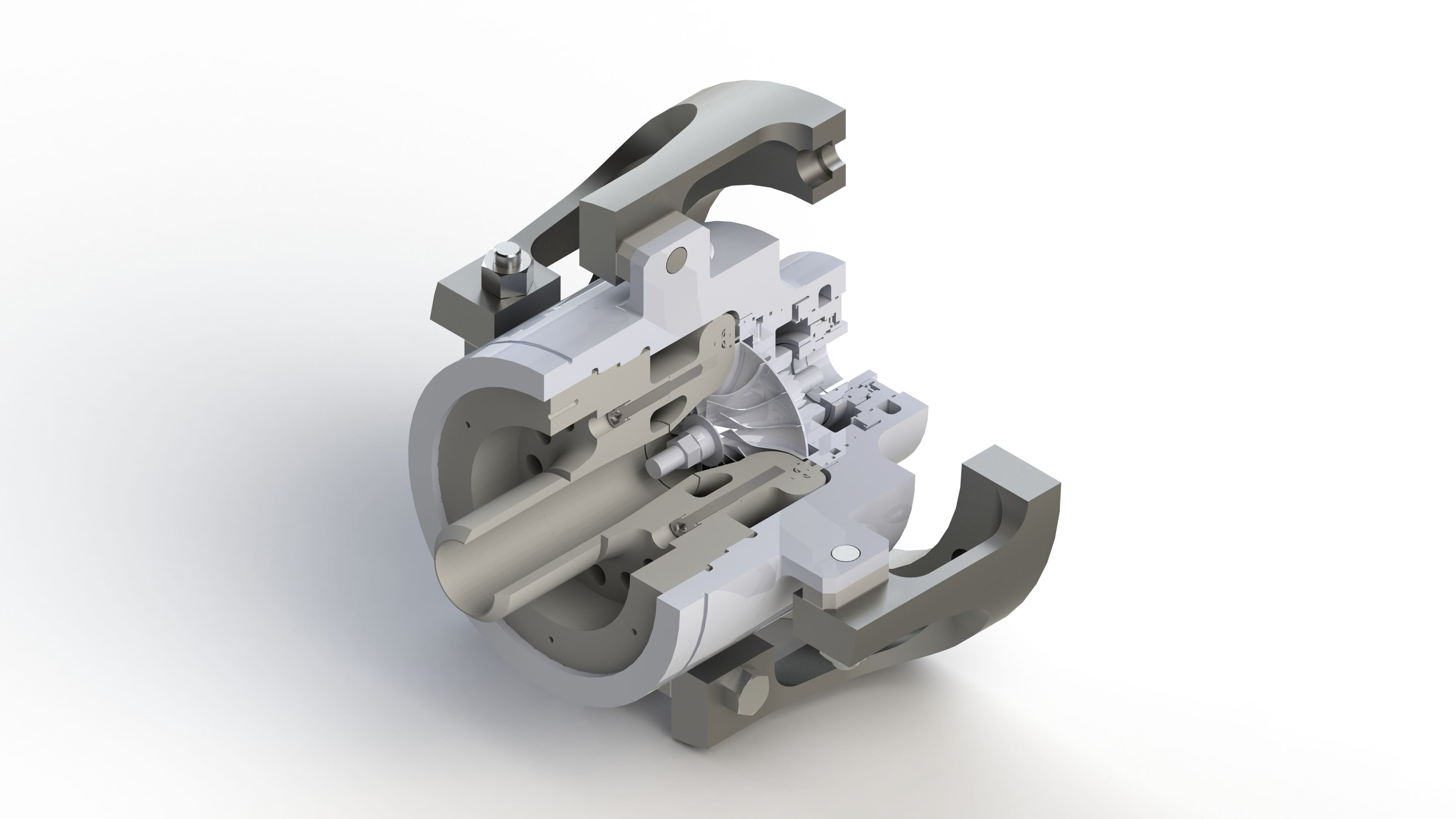
While working for The Centre for Energy Futures at The University of Queensland (formerly known as Renewable Energy Conversion Centre of Excellence), I was involved in the research and design of various energy generation hardware. Some of the things I helped research and design included parts of the High Pressure Test Loop (HPL) at UQ's Renewable Power Generation Lab (UQ RPGL) (ref. Fig 1), a new outboard flow control system (FCP) for the aforementioned High Pressure Test Loop (ref. Fig 2), and parts of a new sCO2 Turbine concept for the Australian Solar Thermal Research Institute (ASTRI) power systems program (ref. Fig 4).
My work on the HPL was primarily based on CAD (SolidWorks 2015). To be specific, it involved me updating the existing model to more accurately represent the status of the HPL as at July, 2019. I had to design new piping runs, design/source new parts fitted along the loop (such as flanges, pipe fittings, and sensors). While I didn't have to do much research on this task, I was exposed to the world of process piping and component selection and design (e.g. the difference between tubing and piping, tapered threads flange sizing etc).
Fig 1 - High Pressure Test Loop at UQ RPGL
My work with the FCP had a little bit more depth than with the HPL - I was involved in the entire design process, from ideation to analysis of the proposed design. The ideation/design started with having to use relevant standards for process piping (ASME B31.3 & AS4041). This involved performing calculations for piping thickness selection and conducting a flexibility analysis (using FEA/ANSYS) to ensure the piping runs wouldn't fail during operation. In the end, my proposed design was accepted with minimal modifications and manufactured (ref Fig 3).
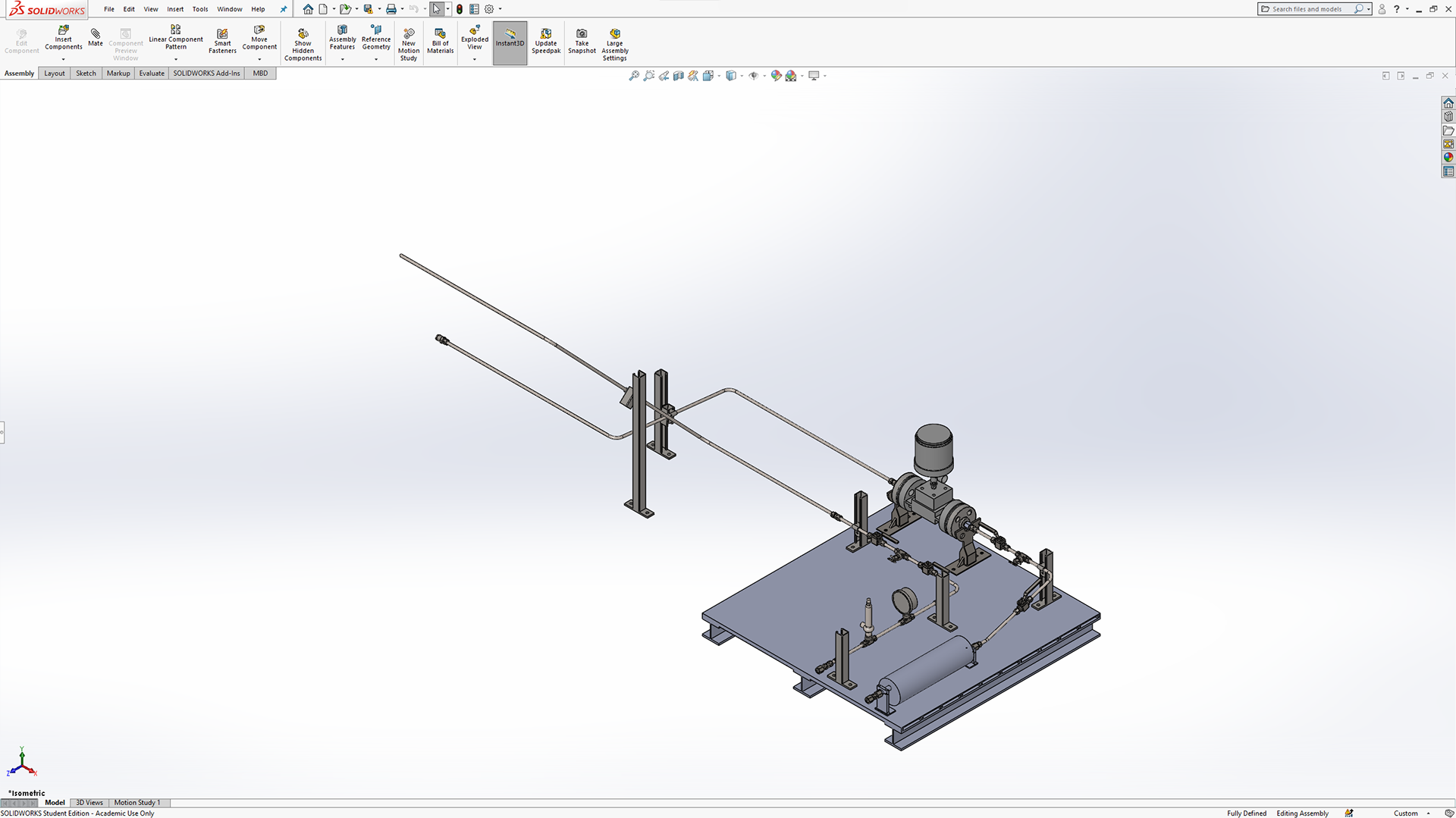
Fig 2 - Outboard Flow Control System for use with the HPL
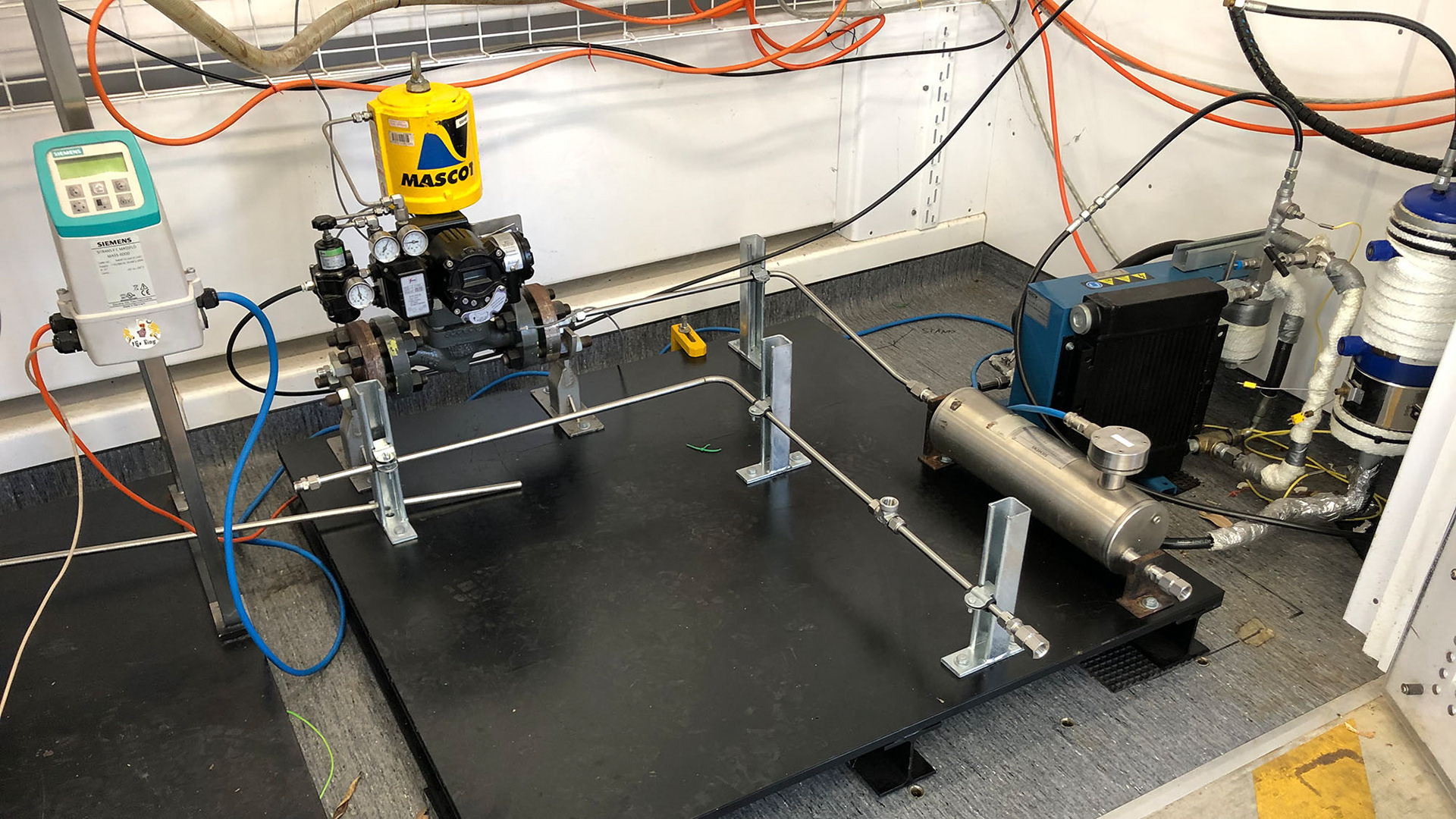
Fig 3 - FCP being assembled at the RPGL
My final and biggest project with the Centre for Energy Futures was conducting research and design work for their participation in the the Australian Solar Thermal Research Institute (ASTRI) power systems program. During this project I obtained a lot of R&D experience and insider knowledge of the energy industry and power generation hardware. My primary objective here was to co-develop and analyse casing/supports designs for sCO2 turbine concepts, with the analysis aspect consisting of a lot of thermal and structural studies. At the time of writing this post, this project was the most challenging one I had been involved in, as sCO2 power cycle/turbine design was an emerging field and there were very limited real-life examples of such designs.
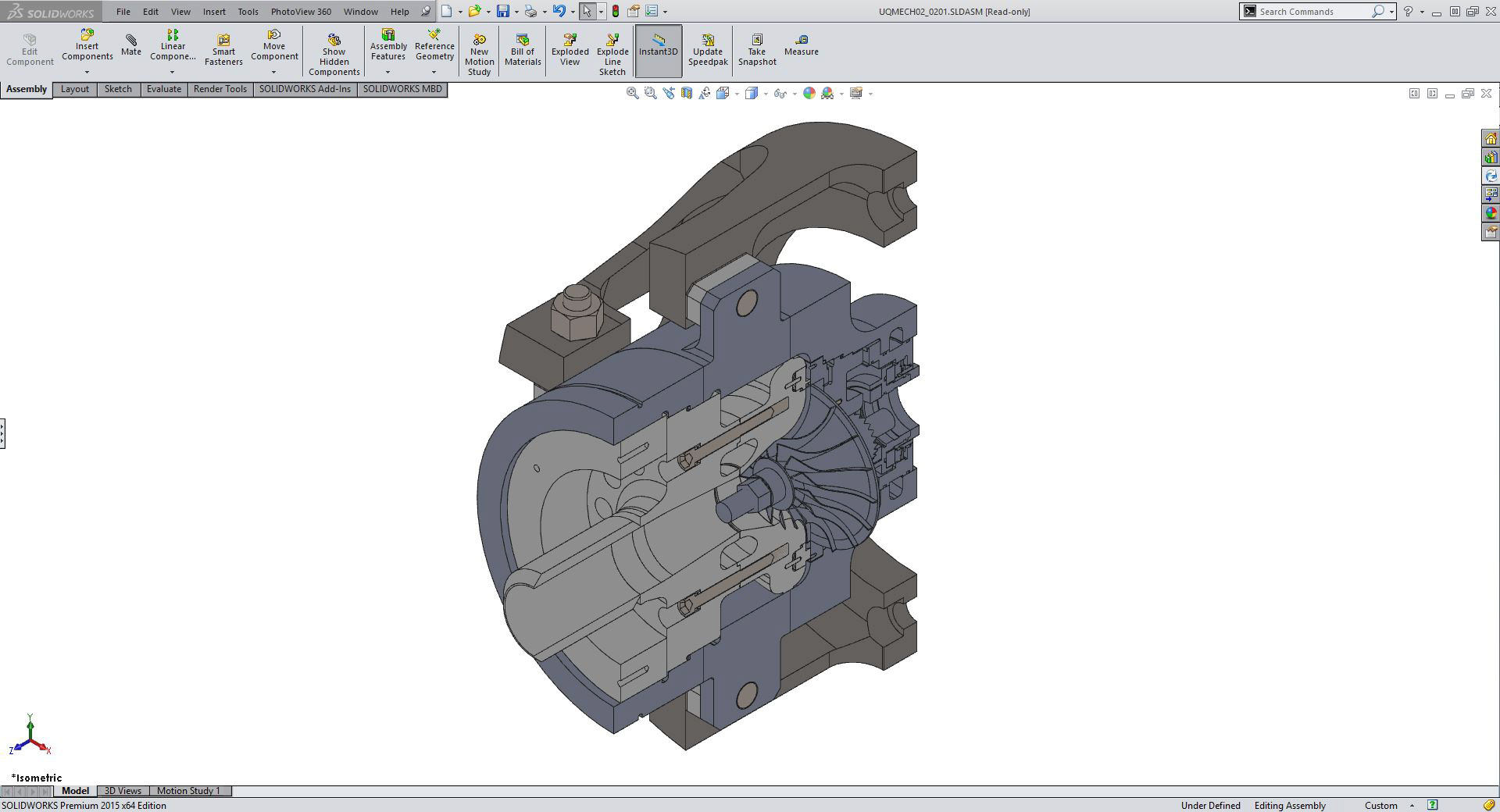
Fig 4 - One of Centre for Energy Futures' proposed sCO2 Turbine Concepts for ASTRI
Nomenclature
In order of appearance in the post,
HPL - High Pressure Test Loop
UQ RPGL - The University of Queensland's Renewable Power Generation Lab
FCP - Outboard Flow Control System for the High Pressure Test Loop